ONE hundred trains returned consecutively to traffic without a single fault, thanks to ‘pit-stop’ servicing techniques. That’s the proud achievement of Alstom’s Manchester Longsight Traincare Centre.
The ‘100 not out’ local depot target has given Longsight, primarily responsible for Pendolino maintenance, a significant benchmark.
Emerging from his work beneath a complete Pendolino lifted for bogie checks, Barry Tetlow, production manager, heavy maintenance, is justly proud of his depot’s record of trains outshopped on target.
“It’s an achievement made easier by no longer having to trek to and from the stores to get parts we need,” he said.
The historic depot, dating from the age of steam, has already seen major transformation from loco and coaches to full Pendolino overhaul. Now it is set for the even greater challenges of the West Coast VHF timetable, bringing faster and more frequent services from next month.
The man in charge since 2003 is traincare centre manager Terry Sherliker, who also manages Alstom’s Liverpool Edge Hill Centre. Much of his railway engineering career has been devoted to major projects in the Far East and South Africa, and he was depot manager at Chester before arriving at Longsight.
“For VHF we have to provide 47 Pendolinos for service each day – one more than at present – but after 18 months’ preparation we’re ready for the challenge,” he said.
With three trains an hour between London, Birmingham and Manchester, as well as more intensive weekend services, exam and overhaul schedules will be revised and adjusted to meet quicker accumulation of mileages and tighter maintenance turnarounds.
“We’ve borrowed the concept of pit-stop servicing from the world of motor racing to cut train downtime,” said Terry. “Vital everyday components such as brake pads and windscreen wipers are now kept where they’re needed, alongside the servicing roads instead of in central stores, saving us up to an hour on each routine job. And development of in-depot repair of components such as air-conditioning units and cardan shafts cuts maintenance time and costs.”
In use since the 1860s, Manchester Long-sight may not have the advantages of brand new depots such as Hitachi, Ashford and Eurostar’s Temple Mills, but has learnt valuable lessons from them.
“We’ve been made very welcome during our visits there, and have certainly put a number of their ideas to good use,” said Terry.
“We’ve even won a national award for our innovative maintenance control processes, carried out in co-operation with West Coast sister depots at Wembley, Oxley in Wolverhampton, Liverpool and Glasgow.”
Major civil engineering work is creating additional new cleaning and toilet discharge sidings that can deal with a whole train at once and, combined with upgrading of existing facilities, will enable each Pendolino to be emptied every day – double the present frequency.
Already busy with CrossCountry Voyagers, Northern Rail Class 323 EMUs and Virgin Trains’ Class 57 Thunderbird locos, Longsight is set for further expansion to accommodate 11-car Pendolinos from 2011.
“Because we have always encouraged our team to build confidence through training courses and NVQ programmes, and worked closely together on changing hours and rosters, they embrace rather than fear change. So we are ready and eager to meet the challenges of the future,” said Terry.
Also preparing for more intensive services next year is Southeastern and its new £35 million maintenance depot at Ramsgate in Kent.
The depot will be instrumental in speeding up work on the Class 375 Electrostar fleet, which will be running up significantly higher mileages and spending more time out on the tracks.
Opened last month by South Thanet MP Stephen Ladyman, the three-road, high-tech shed took two years to complete and complements existing facilities at the depot.
Equipped with state-of-the-art Italian jacking gear, a four-car Electrostar can now be raised as a complete set for bogie exchange, saving a day-and-a-half on the former method of crane-lifting individual coaches.
Team leader Ray Atkinson said: “As well as valuable time saving, it’s a far kinder working environment for the lads, with much less risk of back strain and bumped heads.”
Also, the job has been made easier with equipment such as scissor lifts to gain access to vehicle roofs.
Warranty commercial manager Doug Bowers explained the need for continuous training for the depot team. “Not only do we train comprehensively in use of the new equipment, but maintenance demands change and increase as the trains age and accumulate high mileages,” he said.
A significant, somewhat disheartening, and never decreasing workload results from vandalism, and Southeastern’s 112 Electrostars need constant attention to replace vandalised windows and repair interior and graffiti damage.
“It’s a sad fact of life, but the work has to be done,” said team leader, damage and vandalism, Mark Gibbons.
“But at least we’ve now got the best of working conditions to get the job done quickly and get tidy trains back into service.”
Revved up and ready to go
4th November 2008
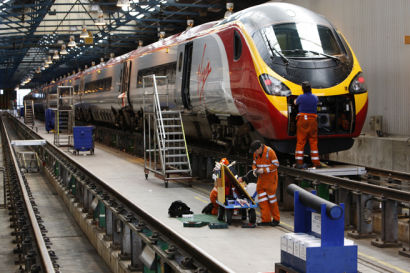